New process and hotel platform on Valhall

According to the original plan for development and operation (PDO) approved by the Storting (parliament) in 1977, Valhall was to cease production around 2000. However, reservoir knowledge and technology had improved so much by the time the new millennium dawned that the licensees could see it would remain on stream far beyond then.
Valhall VRD
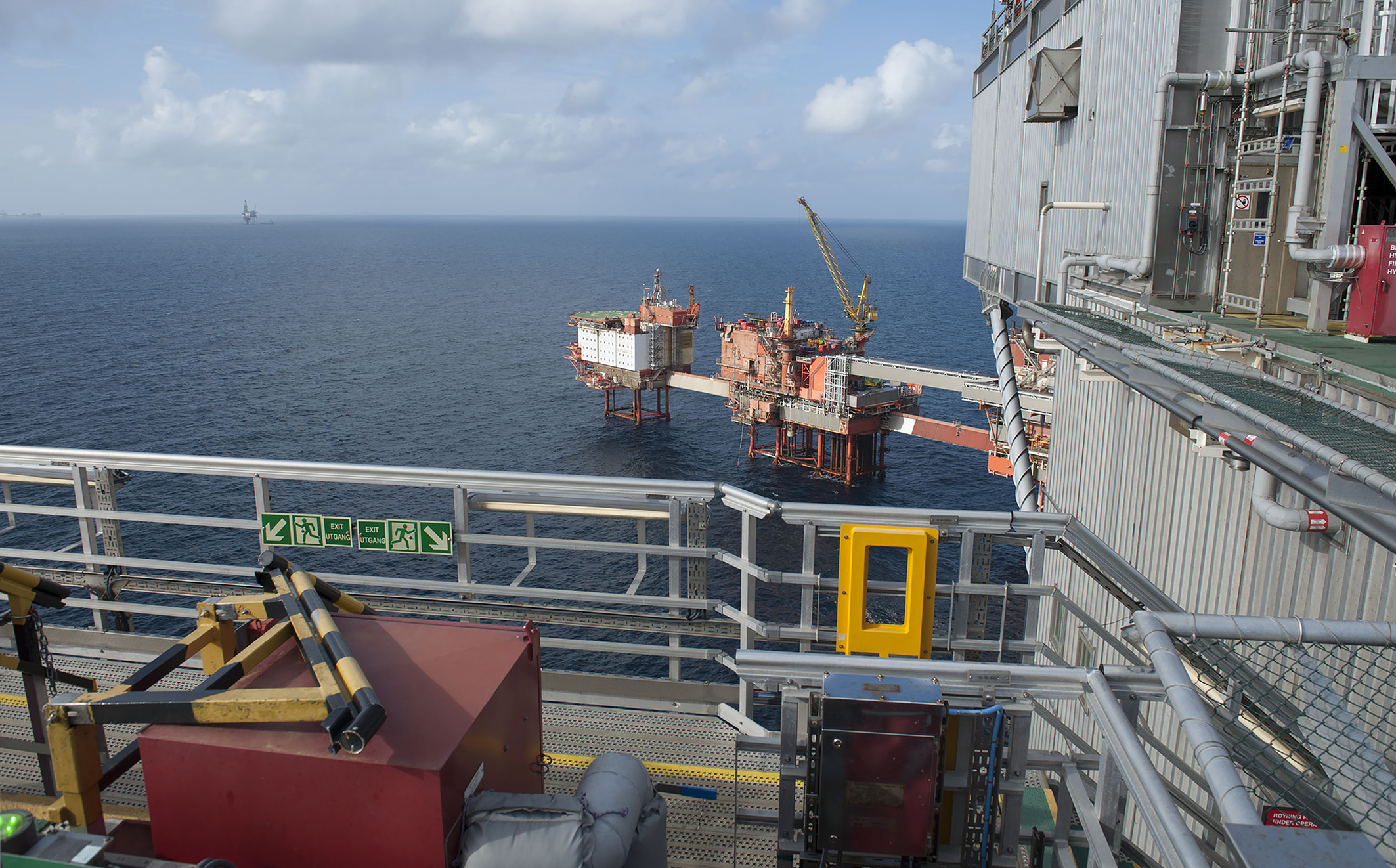
The new process and hotel (Valhall PH) platform represented an important element in the VRD project, which had its PDO approved by the Council of State on 25 May 2007. Planning for the development began around 2000, and first impact assessment programme was presented for consultation on 24 June 2002. The background to work on the VRD was the subsidence of the seabed on the field, along with the approaching end of the approved design lives for existing platforms and equipment. According to the original PDO, the first three Valhall installations would exceed their intended period of production in 2007. BP accordingly had to apply to the Norwegian Petroleum Directorate (NPD) – now the Petroleum Safety Authority Norway (PSA) – in the 1990s for extensions to their producing lives. It received official consent to continue using the quarters (QP) and process and compression (PCP) platforms beyond their original “sell-by” dates.
The VRD project advanced slowly, so such applications needed to be made several times and the installations had to be evacuated on safety grounds if high waves threatened during bad weather.
Almost immediately, the time available for planning came under pressure after a big wave battered several platforms in the Valhall field centre in November 2006. Extensive damage, including the destruction of two lifeboats, was a sharp reminder of the problems posed by seabed subsidence. The VRD was accelerated under big pressure to finish quickly. Jacking up and modernising the older platforms were studied, but the choice fell on a completely new installation. While this would be costly to build and install, spending on operation and maintenance could be cut. Constructing separate facilities for quarters and processing was assessed for safety reasons. However, the licensees opted for a combined structure which could be made sufficiently safe.[REMOVE]Fotnote: Teknisk Ukeblad , April 2005, “Valhall elektrifiseres”. The view was that a new platform would be easier to tailor for future needs on the field, and have a longer expected producing life.
A decision was also taken in 2005 to convert Valhall for operation by power from shore, and this was taken into account when specifying and planning the PH platform. The installation process was to take place while the existing facilities remained in full operation, with any necessary shutdown confined to the hook-up and commissioning phase. According to the 2007 PDO, the new structure would come on stream in November 2010. But the actual start date was delayed until 26 January 2013. The platform itself had been positioned at the field centre as early as 2009, almost three years earlier. So the question is why the installation phase took as long as it did.
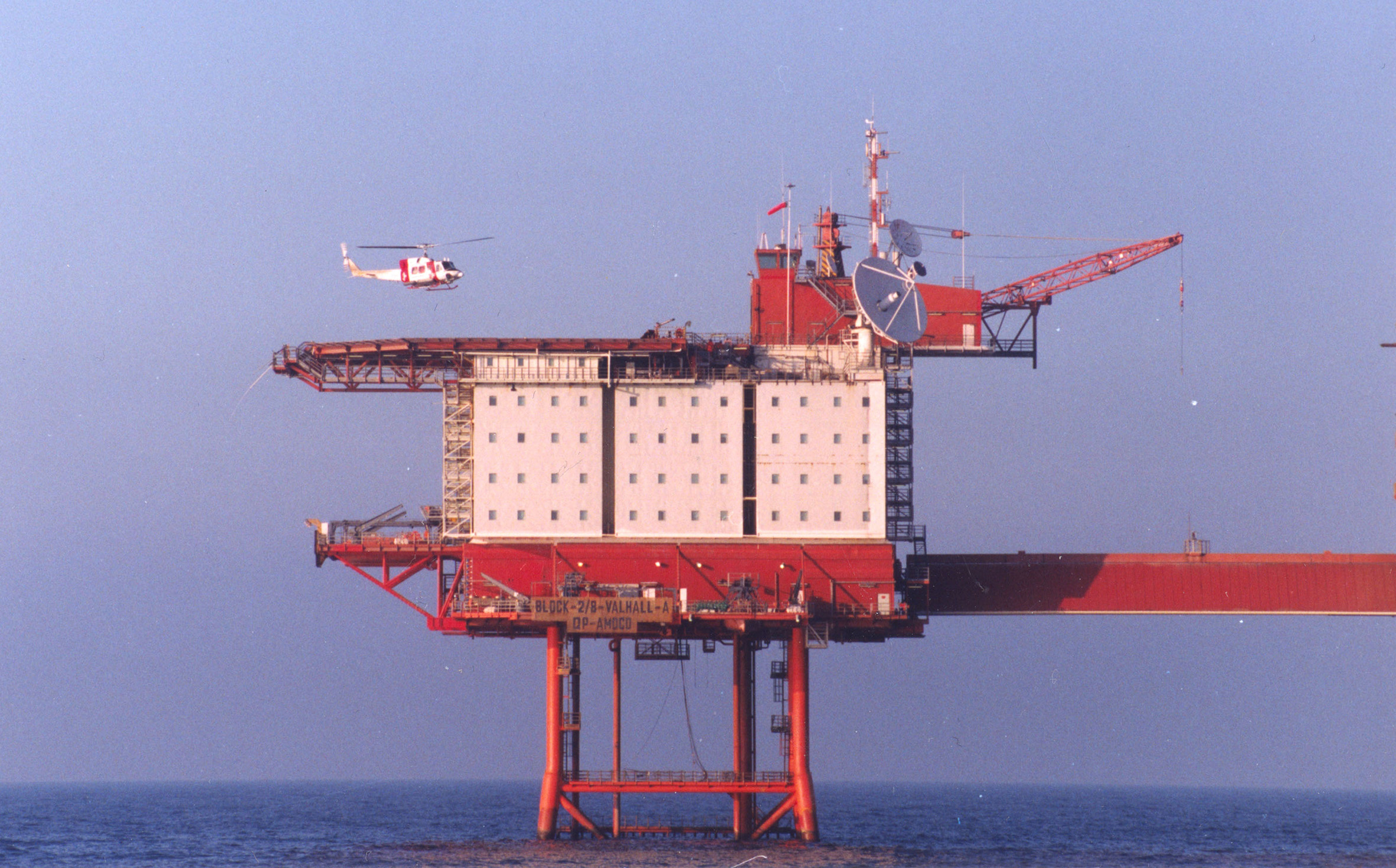
Valhall PH was intended to replace the functions of the existing QP and PCP facilities. The latter was shut down for the last time on 29 July 2012. This meant that the field was off stream for just over six months compared with a planned three. This time was used in part to transfer pipeline connections from the PCP to the PH platform.[REMOVE]Fotnote: BP Norge, Utslippsrapport for Valhallfeltet og Hod 2012 , 8. The process facility for the new installation was designed by Mustang Engineering in Houston, Texas, while Fabricom in Stavanger handled design of the quarters module.
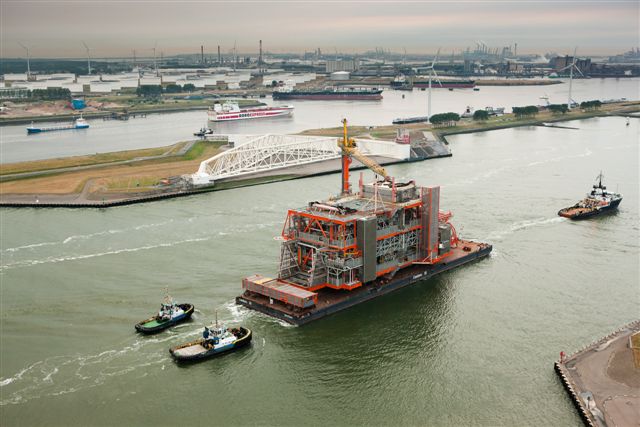
Construction of Valhall PH was handled in several locations, with the support structure (jacket) assembled at Aker Kværner Verdal north of Trondheim. The quarters module was fabricated at Lowestoft in the UK, while Heerema in the Netherlands handled fabrication and assembly of the topside. Others included ABB, which installed systems for power from shore, and Subsea 7 for all pipework – including reconnections. About 45 per cent of the contracts went to Norwegian suppliers. The steel jacket was lifted into place by the Saipem 7000 crane ship in June 2009, while the topside with several modules followed in the summer of 2010. A bridge connects to the injection platform (Valhall IP). Taken into use during the spring of 2011, the quarters module includes control room, technical and work rooms, stores, canteen, lounges and 180 one-berth cabins.
Challenges related to delivery of the quarters module and the scope of work involved in reconnecting to the new process facilities meant that the project had to be rescheduled.[REMOVE]Fotnote: Petroleum Safety Authority Norway, 21 May 2010, “BP Norge AS (BP) har fått samtykke til bruk av QP og PCP på Valhall utover designlevetid”. An evaluation report from the NPD concluded that insufficient time and inadequate resources had been allocated for planning in the early phase of the project.[REMOVE]Fotnote: Norwegian Petroleum Directorate, Stavanger, 2013, Vurdering av gjennomførte prosjekter på norsk sokkel. This meant in part that the dimensions and weight of Valhall PH had to be adjusted several times during the fabrication process. Compared with the PDO estimates, costs overran by 62 per cent for platform construction and installation and by 327 per cent for wells. One reason for these increases was that work on integrating the new and old installations became more extensive than originally planned. In addition, the Valhall reservoir proved more complex than had been expected in the PDO. That called for more wells, while drilling costs per well also rose.
Power from shore
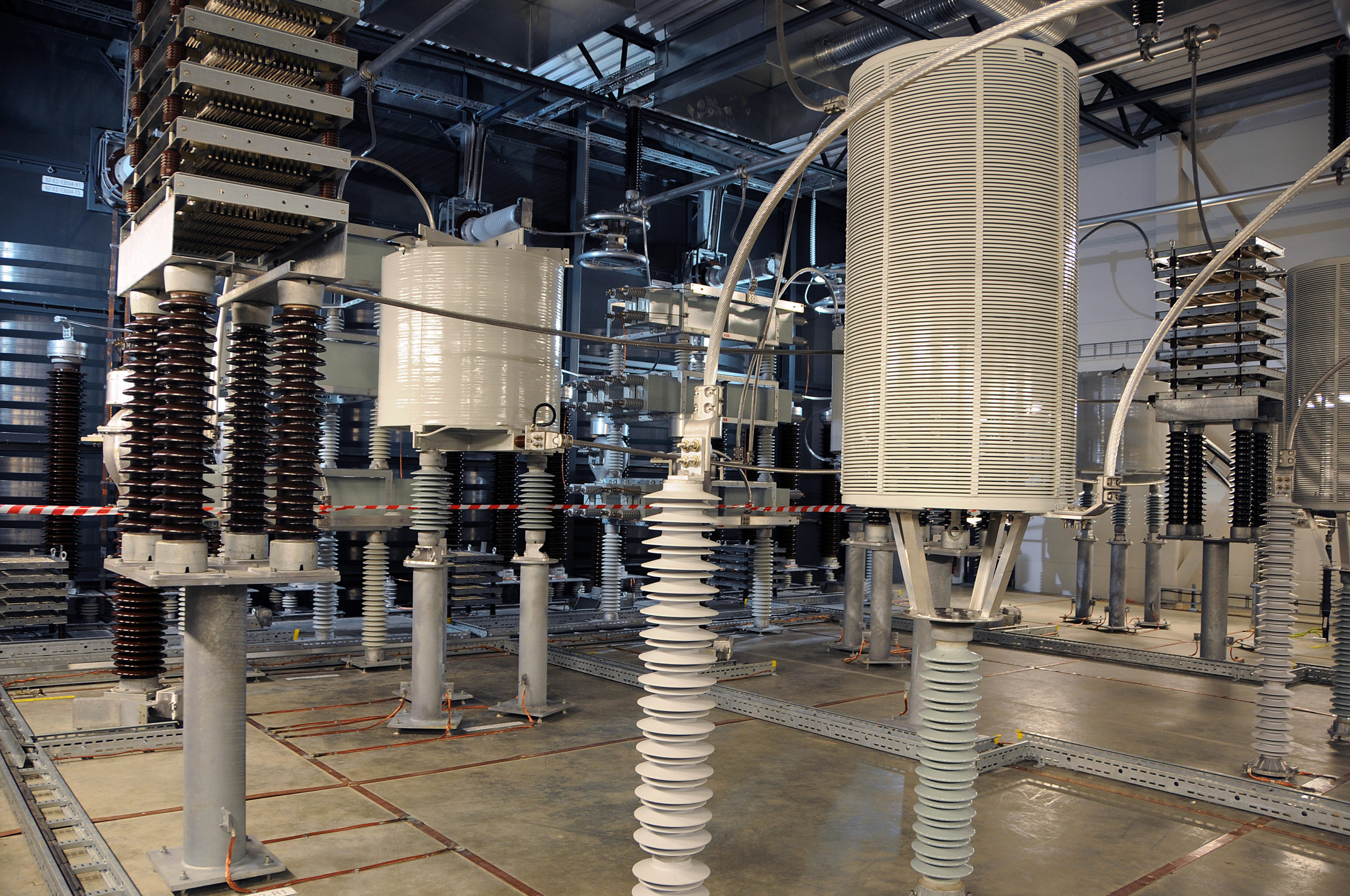
Several benefits were achieved by bringing hydroelectricity from land through a submarine cable and shutting down the local generators which had previously supplied the platforms with power. Emissions to the air were reduced by eliminating the gas turbines. Hazards from burning gas as fuel were removed, and other discharges from the platforms are injected into the sub-surface.[REMOVE]Fotnote: Rasen, Bjørn (2007): LF6A. Valhall at 25 … and it’s only the beginning , 202. The platforms also experienced less noise and vibration, while eliminating exhaust fumes improved the environment for those on board. Read more in article “Power from shore to Valhall“.
Control rooms offshore and on land
The control room on the PCP was situated virtually in the centre of the structure, and had to be evacuated on occasion because of the threat of an explosion. Its replacement on Valhall PH is located behind a fire- and explosion-proof wall in the hotel section, allowing it to remain operational even if incidents occur in production areas. Should an emergency arise, moreover, operations can also be controlled remotely from a parallel control room on land, using a fibreoptic cable laid in parallel with the power line.[REMOVE]Fotnote: Rasen, Bjørn (2007): LF6A. Valhall at 25 … and it’s only the beginning , 203. This cable supports substantial data transfer, and a number of platform operations can be remotely controlled. Continuous transmission of sound and images is also possible between the control rooms. While the PCP needed about 100 personnel for normal operations other than drilling, Valhall PH can usually be run by about 20 people offshore thanks to the fixed data link.
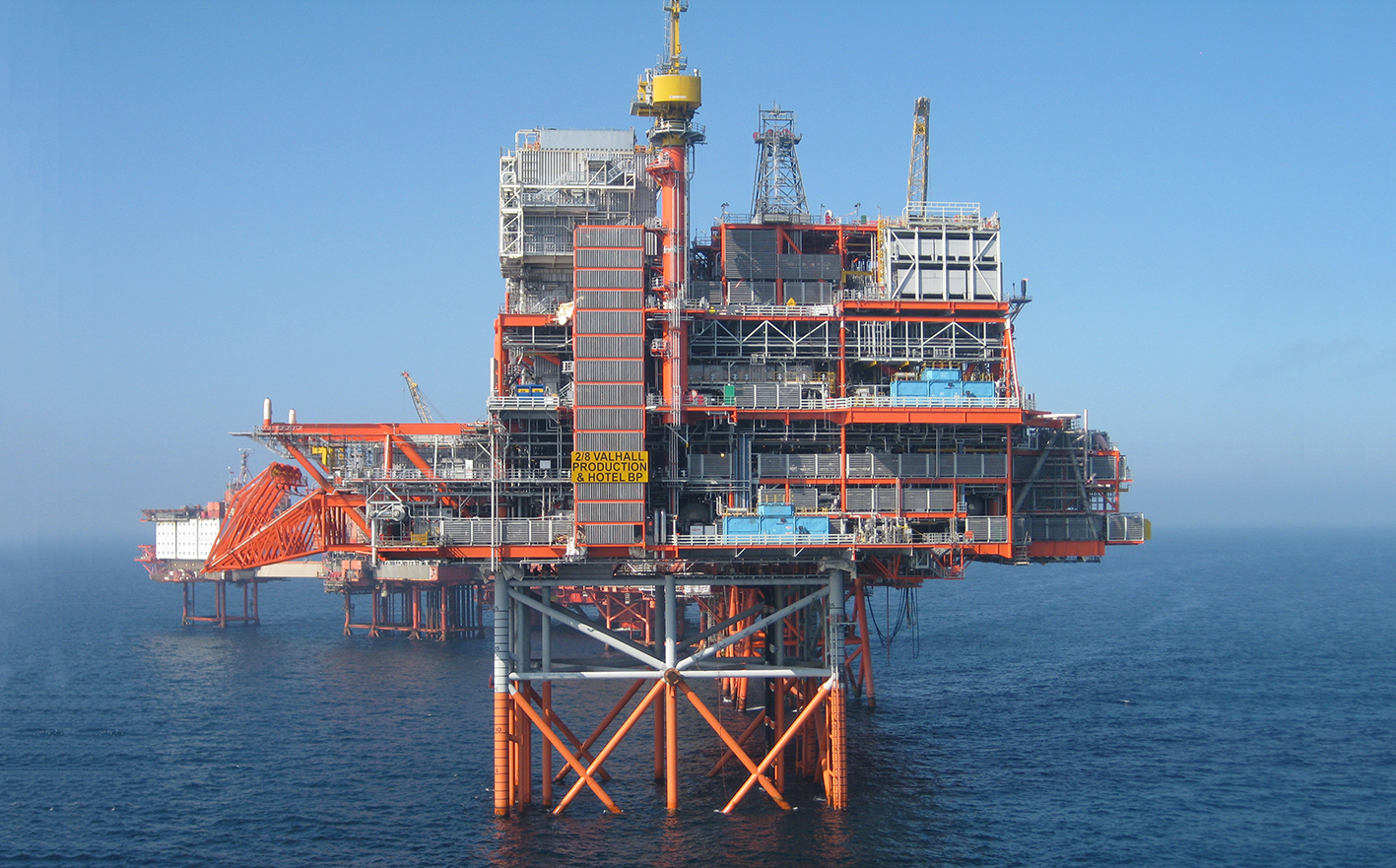
Read more in the articles about
New platform – new processPower from shore to Valhall