Valhall orders for crisis-hit yards

But the Yom Kippur War between Israel and its neighbours in October 1973 marked a turning point. This conflict prompted the Organisation of the Petroleum Exporting Countries (Opec) to impose a boycott on oil sales to Israel’s supporters.
Crude prices quadrupled, demand for oil slumped and tanker freight rates fell dramatically. Most observers at the time believed the crisis would be short-lived, but were proved wrong.
Instead, it lasted for years. The decline in oil trading meant insufficient work for the global tanker fleet, and the position steadily worsened as new ships entered the market. Shipowners, banks and other credit institutions suffered big losses.
Shipyard jobs at risk
The Swedish shipbuilding industry went more or less out of business. Competition from the Far East was particularly tough. Yards in Japan, Taiwan and Korea offered prices 30-45 per cent below those of their European rivals.The collapse in tanker shipping sparked a deep crisis in the shipbuilding industry worldwide. From having contracts for several years to come, the yards quickly found themselves with virtually empty order books.
Norwegian builders were also hit – particularly the Aker group. This was not least because Norwegian shipowner Hilmar Reksten cancelled orders for four supertankers at the group’s Stord Verft subsidiary south of Bergen. Construction of a new dry dock for such vessels at the yard had to be halted.[REMOVE]Fotnote: Nerheim, G, Jøssang, L G, and Utne, B S, I vekst og forandring. Rosenberg verft 100 år, 1896–1996 (1995), 350-352.
Compared with the dramatic shipbuilding cutbacks in other countries, Norway’s yards were nevertheless fortunate. The oil industry was expanding, and needed fabrication services.
Yard after yard converted from building ships to offshore work. Aker Stord, for example, won the contract to fabricate and hook up modules for the Statfjord A platform topside – a job it completed in May 1977.
That spring, much attention focused on whether development of Valhall and Hod would provide new orders for Norwegian yards. Three thousand jobs at Aker’s Verdal and Stord facilities were threatened unless fresh work turned up.
Aker felt that the authorities took too long to give formal approval to new developments on the Norwegian continental shelf (NCS).[REMOVE]Fotnote: VG, 3 March 1977, “3000 ansatte i fare”. But the delay arose primarily because the operator first had to find an export solution.
Amoco negotiated with Statoil and the Phillips group on a tie-in Ekofisk to the existing pipelines for landing oil and gas. Only when this challenge had been overcome could development plans for Valhall and Hod be submitted to the government and the Storting (parliament). (See the article on the riser platform.)
Blowout creates uncertainty
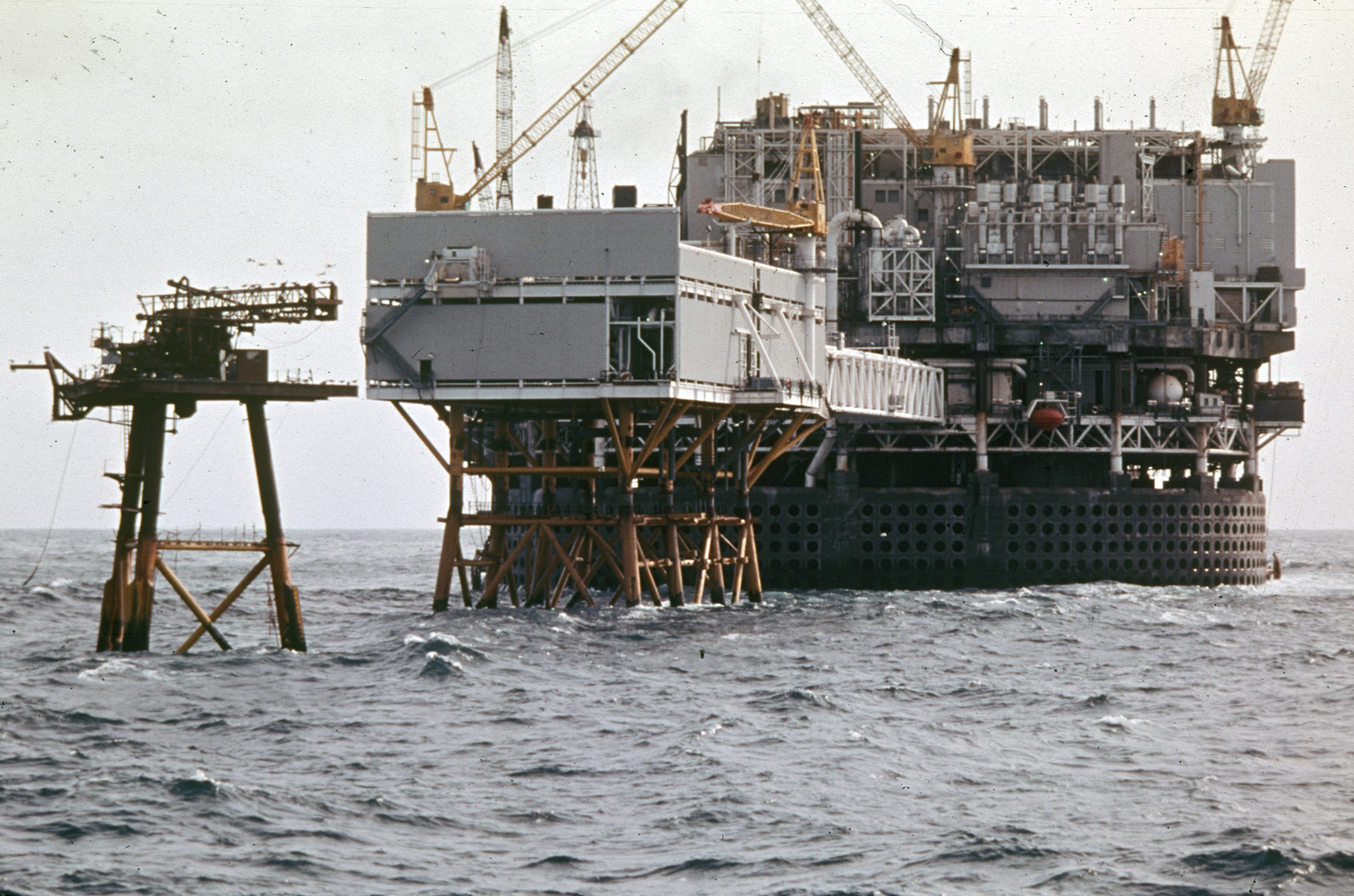
These proposals were approved on 21 April 1977. At 22.00 on the following day, an uncontrolled blowout occurred from well B-14 on the Ekofisk field.
This major and unexpected accident attracted much attention worldwide. Preparations for responding to oil spills proved virtually useless, with only 1 000 tonnes recovered. Fortunately, the rest of the oil deteriorated before reaching land.[REMOVE]Fotnote: www.kulturminne-ekofisk.no Known as the Bravo blowout, from the platform where it happened, this incident spurted large quantities of oil and gas five-six metres into the air. Some 9 500 tonnes of crude cascaded into the sea over the next seven and a half days.
The Bravo incident was the first major blowout on the NCS, and so far the only one. But the question at the time was whether it would have consequences for the Valhall development.
Industry minister Bjartmar Gjerde reported to the Storting on the Bravo blowout on 2 June. He faced criticism, first and foremost from Reidar T Larsen of the Socialist Left (SV) party, who asked how it was possible to continue as if nothing had happened after such an incident.
“The SV cannot have confidence in an oil policy which does not give safety needs and oil spill response priority ahead of other considerations,” he said, and called for a change in oil policy.
Labour premier Odvar Nordli wondered whether this should be regarded as a vote of no confidence, but that was denied. The motion only received backing from the SV and Hans Hammond Rossback of the Liberal Party.
A fault line in Norwegian oil policy had thereby been clearly revealed, but the critics failed to win support and the main principles governing this industry remained unchanged.
In the debate on Valhall and Hod, Lauritz B Sirevaag, a Conservative representative from Rogaland (the county which includes Stavanger), observed:
“Although it would be appropriate to exercise some caution and reserve after the Bravo accident, crucial emphasis must be placed on activity in the North Sea being maintained and given a continuity which can safeguard jobs, industrial progress and regional development.”[REMOVE]Fotnote: Stavanger Aftenblad , 3 June 1977, “Valhall og Hod skal bygges ut”.
At a time characterised by growing unemployment, cross-party agreement prevailed that it was important and right to secure work for domestic companies on the NCS.
The final oil debate in the Storting before the 1977 summer recess accordingly resolved that the Valhall and Hod development could continue as planned.
However, the announcement and award of new offshore blocks was postponed until the autumn, and oil exploration above the 62nd parallel (the northern boundary of the North Sea) was postponed until further notice.
August Wilhelmsen, chairman of the Federation of Norwegian Engineering Industries (MVL), expressed a degree of optimism on behalf of the sector in the wake of this decision:
“Were Norwegian industry to secure a significant share of deliveries to the development of the Valhall-Hod field, as the licensees have indicated, this would represent a valuable contribution to securing continuous operation at engineering companies particularly involved offshore.”
Most fabricators needed contracts immediately to avoid layoffs or redundancies.[REMOVE]Fotnote: Stavanger Aftenblad , 5 June 1977, “Dystre utsikter for verkstedindustrien”.
Valhall to the rescue
Three platforms – for drilling, quarters and production respectively – were planned for Valhall itself, all with steel jackets (support structures).
A riser platform was also to be installed on Ekofisk to receive the oil and gas pipelines from Valhall. (Read more in the article on developing the Valhall village.)
In its application for permission to land Valhall and Hod production, operator Amoco had undertaken to use at least 50 per cent Norwegian products and services.[REMOVE]Fotnote: Kostnadsanalysen norsk kontinentalsokkel, bind II, 278. That corresponded to orders worth NOK 2 billion in 1977 value, but the question is how realistic this was.
The organisation of the development explains how the orders were placed, with Amoco directly responsible for project management through a staff of about 40 people.
The company was used to conducting engineering design for all its US fields, but the landing application had committed it to utilising Norwegian expertise.
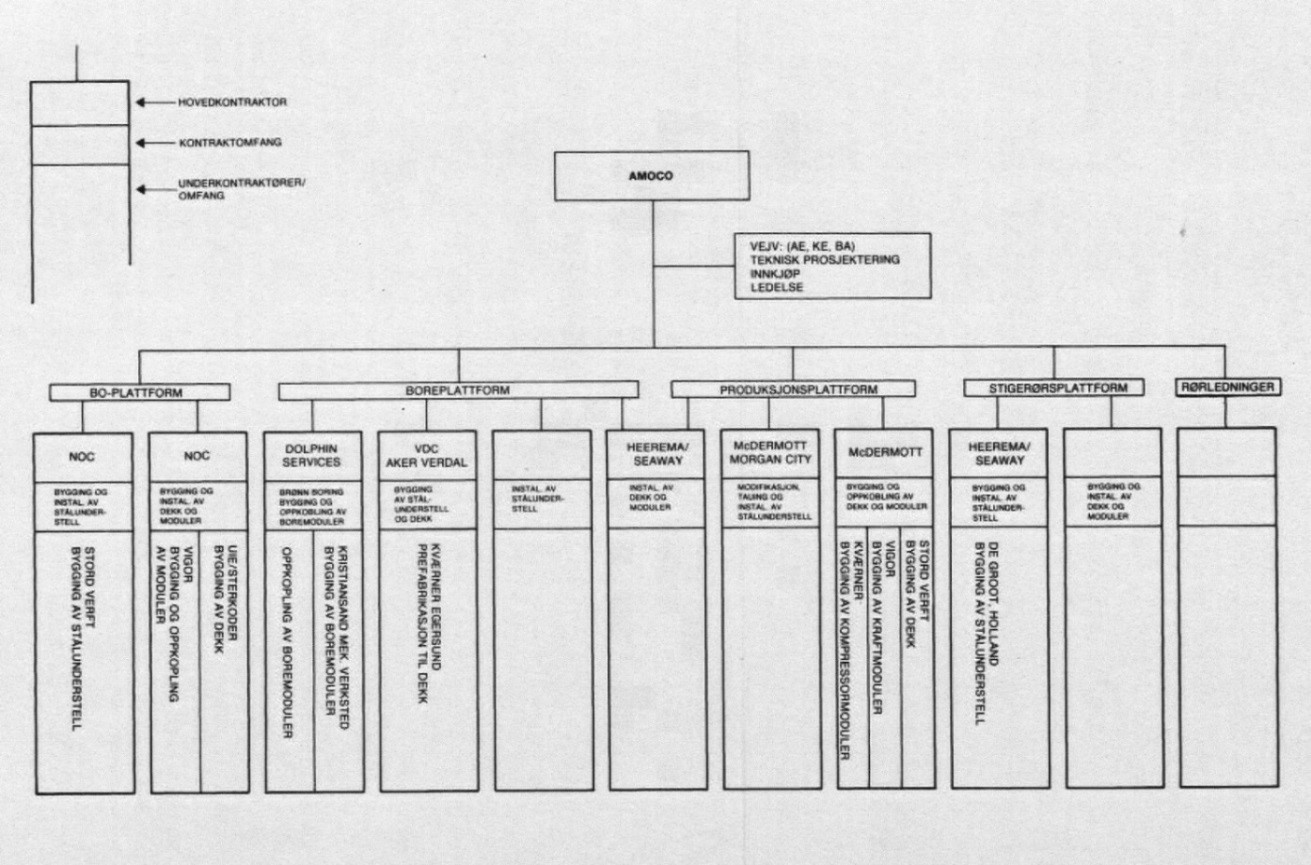
Aker and the rival Kværner group teamed up for a joint bid, and negotiations resulted in them setting up a partnership with Brownaker Offshore A/S under the name Valhall Engineering Joint Venture (VEJV).
Brownaker – a partnership between Aker and the UK arm of USA’s Brown & Root group – was included at Amoco’s insistence. It felt that additional offshore design capabilities were required to supplement the expertise of the Norwegian companies.[REMOVE]Fotnote: Kostnadsanalysen norsk kontinentalsokkel, bind II, 231-234.
The assignment was split between A/S Akers mek Verksted (41.7 per cent), Brownaker Offshore A/S (25 per cent), and Fred Olsen & Co and Kværner Brug A/S (33.3 per cent).
While the VEJV had its head office in Aker Engineering’s premises at Tjuvholmen in Oslo, engineering work was pursued not only there but also at Kvaerner Engineering’s offices in Billingstad outside the capital and at Brown & Root in Houston and London.[REMOVE]Fotnote: Kostnadsanalysen norsk kontinentalsokkel, bind II, 270.
The VEJV was to assist Amoco with engineering design, procurement and management. It would secure the necessary documentation – calculations, drawings and specifications – needed by Amoco to secure government approval and as the basis for the operator’s own assessments.
Administrative procedures, estimates and deadlines were also prepared by the partnership, which additionally handled procurement and reception of equipment and served as Amoco’s consultant during the construction phase. It put together tender packages as the basis for fixed-price contracts.
Each platform had a main contractor responsible for agreements with subcontractors. Amoco awarded a main contract for the drilling platform to McDermott in preference to Brownaker.[REMOVE]Fotnote: Klassekampen , 1 November 1979, “Storoppdrag i Nordsjøen. Norge får smulene”.
The licence terms stated that Norwegian companies were to be given preference provided they were competitive. Almost as “compensation”, Aker and Kværner were awarded the fabrication jobs and formed a joint venture called the Valhall Design Consortium (VDC).
Building the jacket went to the Aker Verdal yard north of Trondheim, while Kværner Brug’s Egersund yard south of Stavanger was assigned the topside and the bridge to the quarters platform.
Four topside modules came from Stord Verft and the drilling modules from Kristiansund mek Verksted.[REMOVE]Fotnote: The North Sea Platform Guide, 1985, 688. BP’s website. Kostnadsanalysen norsk kontinentalsokkel,bind II, 275-276. Myklebust, Alf Terje, 75 år på Kjøtteinen: 1919-1994: jubileumsbok for Aker Stord , 1994, 209. Dolphin Services was responsible for hooking up the latter.
McDermott Norge also won the main contract for the production platform , embracing the whole process and compression facility. Brussels-based Oceanic, a subsidiary of McDermott Hudson Inc, was the main contractor for the topside and modules and allocated the fabrication work in turn to three Norwegian yards.
These were Stord Verft (topside), Vigor in Orkanger near Trondheim (generator module) and Kværner Egersund (three compressor modules).
French fabricator UIE was also in the running for the topside contract, but political pressure was applied to ensure that the developer opted for Norwegian suppliers.
The companies were called into the Ministry of Petroleum and Energy, where minister Bjartmar Gjerde explained the difficult employment position at Stord.
No direct order was given about where the topside job was to be placed, but it ended up with Stord Verft. That meant the yard could avoid redundancies.[REMOVE]Fotnote: Aftenposten , 16 November 1979, “500 mill. i Valhall-oppdrag” and BT 16 November 1979, “Stord verft sikret arbeid i hele 1980”.
Netherland Offshore Company (NOC) was the main contractor for the quarters platform (QP). This company was later acquired by McDermott.
Stord Verft landed the job of building the jacket, whilst a joint venture between UIE and Sterkoder mek Verksted in Kristiansund fabricated the topside. Vigor produced the modules and hooked them up.[REMOVE]Fotnote: Kostnadsanalysen norsk kontinentalsokkel, bind II, 275-276.
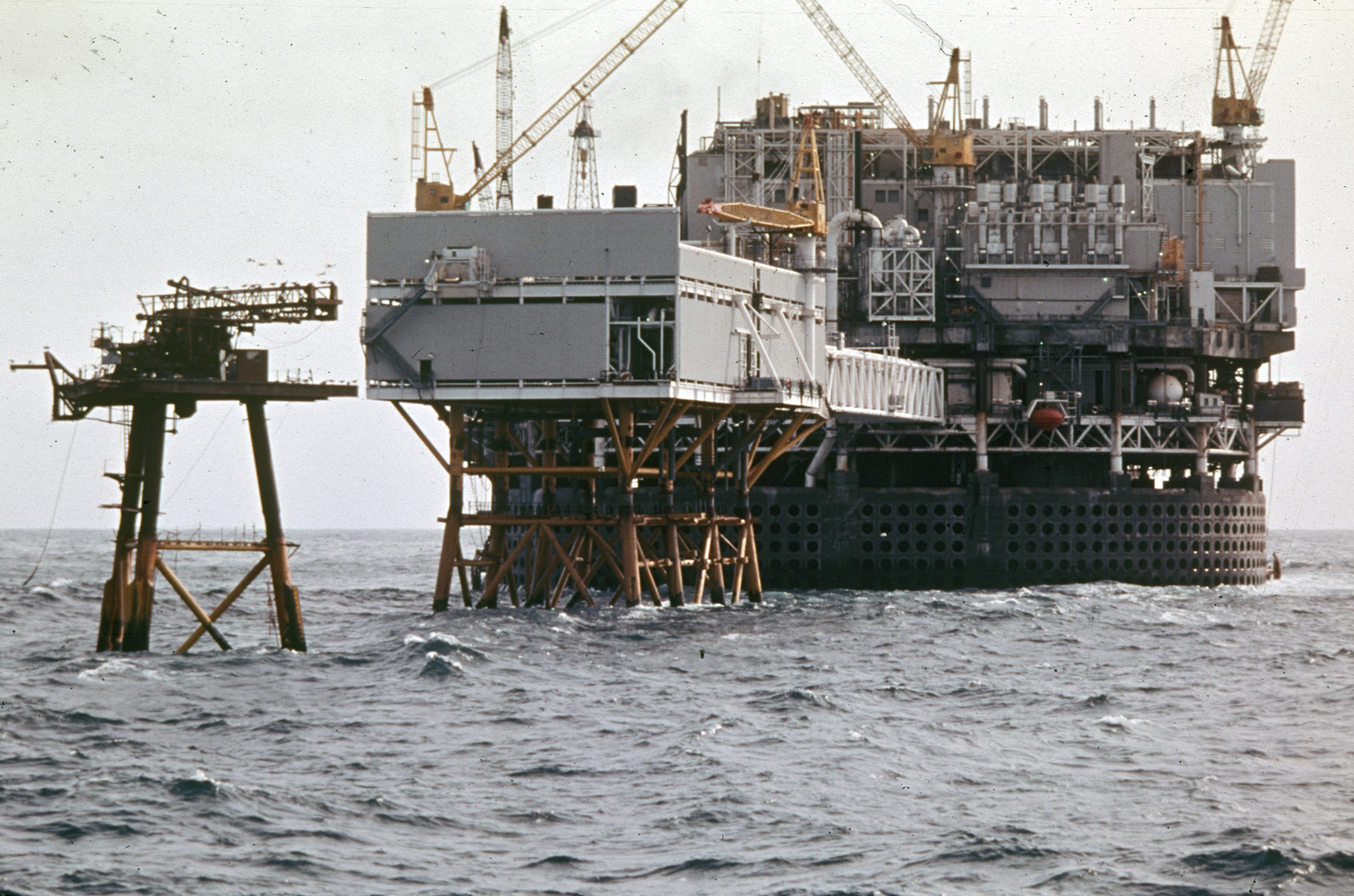
The Ekofisk 2/4 R riser platform was built with a bridge which carried piping systems across to the 2/4 T Ekofisk tank. While the bridge and topside were fabricated at Aker Verdal, Heerema/Seaway was main contractor for the jacket and gave Dutch DeGroot the job of building it.
Assessment
A study was conducted while the development was under way by an official commission of enquiry and published as an analysis of costs on the NCS (Kostnadsanalysen norsk kontinentalsokkel).
This appeared before the Valhall project had finished, and accordingly contained nothing about the final costs of that development. But a number of conclusions were drawn on the basis of the data available to the commission.
Amoco maintained that the goal of using 50 per cent Norwegian goods and services was difficult to meet, since much of the materials and a lot of the equipment necessarily had to be bought outside Norway.
While domestic firms were involved in much of the construction work, they did not build the steel jackets for the process and riser platforms, for example. Foreign main contractors were used for all four of the installations.
Although purchases of goods and services from Norwegian suppliers failed to meet the original estimate of NOK 2 billion, the domestic contributions were substantial.
Fabricators in Norway entered into contracts worth a total of NOK 700 million, mostly on the basis of the lowest bid. They proved able to tender competitively for all the modules. But the approach chosen for the engineering work was regarded as adding to costs.
Only a few contracts cost more from being awarded in Norway. This overspend totalled NOK 75 million or about 10 per cent of the final bill. The bulk of it related to the Aker and Kværner contract for the drilling platform.
It was emphasised that the figures had to be seen in light of the difficult conditions for Norway’s shipyards, which meant that their prices were driven sharply down. The principal competitors were French and Dutch fabricators.
Another consideration was that foreign suppliers were probably less motivated to compete over deliveries because they were aware of the stipulations concerning Norwegian deliveries.
The Valhall development accordingly threw a lifeline to several Norwegian fabricators engaged in a difficult transition from shipbuilding to offshore contracts following the tanker crisis.
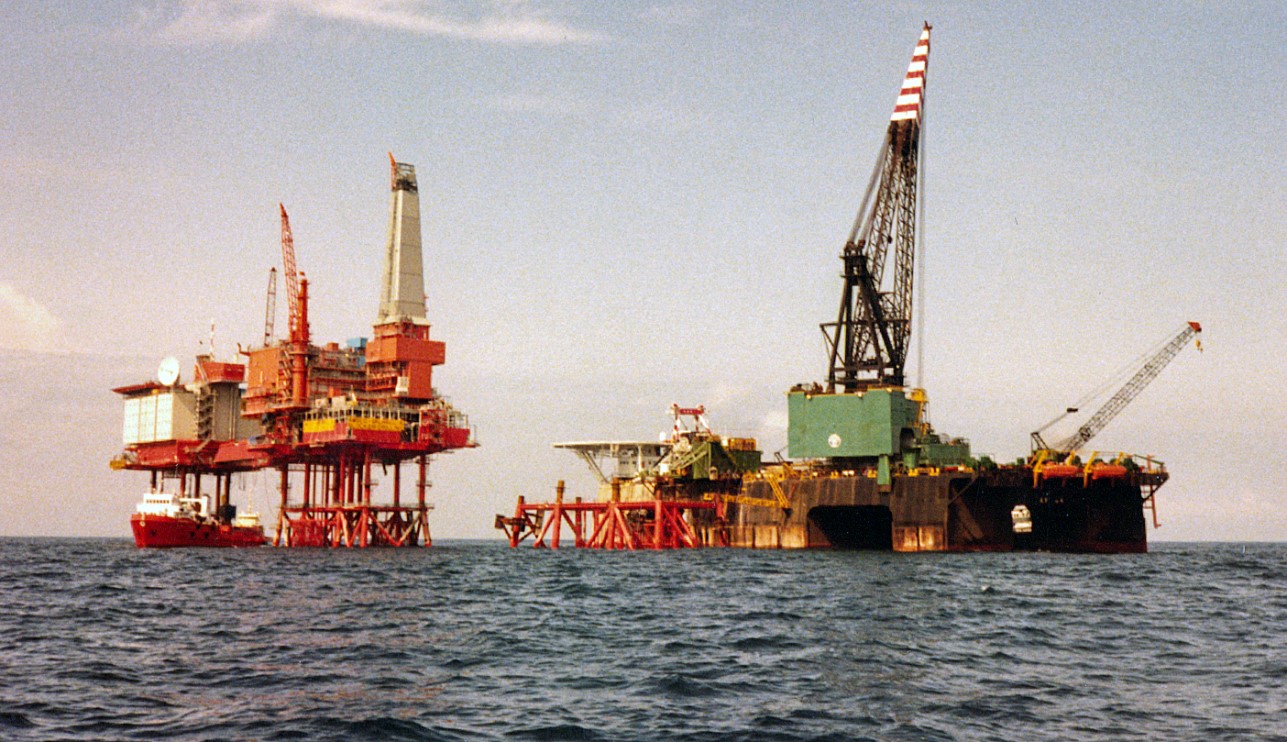
These processes were given solid support by the Norwegian government, partly through provisions which required operators to use domestic goods and services, and partly through mild pressure and urgings from the Ministry of Petroleum and Energy.
The cost analysis report subsequently found that this had little negative effect on spending. Norwegian yards and industrial groups benefited not only from contracts which rescued them financially but also by increasing their offshore expertise. That in turn laid the basis for accepting new assignments from the oil industry.
Developing the Valhall centreFinancing the Valhall development