When the alarm sounds … a selection of incidents on Valhall

March 1976 – fire on Deepsea Saga
A fire broke out on 2 March during the final phase of test drilling on Deepsea Saga . The flames roared high into the air, and the whole rig shook. The drill bit had penetrated a pocket of gas under high pressure. With the string driven out of the well like crumpled spaghetti and the casing cut, the gas ignited to produce an explosive blaze. Forty of the 63-strong crew were evacuated by helicopter to Ekofisk, Sola airport outside Stavanger or standby vessel King Supplier.
The remainder remained on the rig to fight the fire and clean up. Fortunately, the flames were extinguished fairly quickly and nobody was injured. The fire went out once the gas pocket was exhausted. Representatives from the Norwegian police, the Norwegian Petroleum Directorate (NPD) and Amoco investigated the incident.[REMOVE]Fotnote: Rasen, Bjørn (2007): LF6A. Valhall at 25 … and it’s only the beginning , p 68; Norwegian Official Reports (NOU) 1977 no 47, Ukontrollert utblåsing på Bravo 22. april 1977 , p 21.
September 1984 – death on Valhall
A 39-year-old welder died from injuries sustained during maintenance work on Valhall for Bomek A/S. He was installing a cradle on the crown block while standing on scaffolding, and was pushing the cradle into the correct position on the platform deck when the plank he was standing on shifted in the opposite direction.
The victim himself had undone the security clamps and removed one of the boards to access a weld. No defects were discovered in the scaffolding. He fell 11.7 metres onto a deck grating. Both the police and the NPD investigated the incident.[REMOVE]Fotnote: Stavanger Aftenblad , 10 September 1984, “Drept på Valhall”. They found no deficiencies in the equipment or the procedure which raised issues of criminal liability, and neither agency took further action.[REMOVE]Fotnote: Police report, case 7869/84, Stavanger police department’s archive.
The insurance company refused to pay full compensation to the family because it maintained that the worker had behaved negligently.[REMOVE]Fotnote: Rasen, Bjørn (2007): LF6A. Valhall at 25 … and it’s only the beginning , p 151.
June 1985 – fire
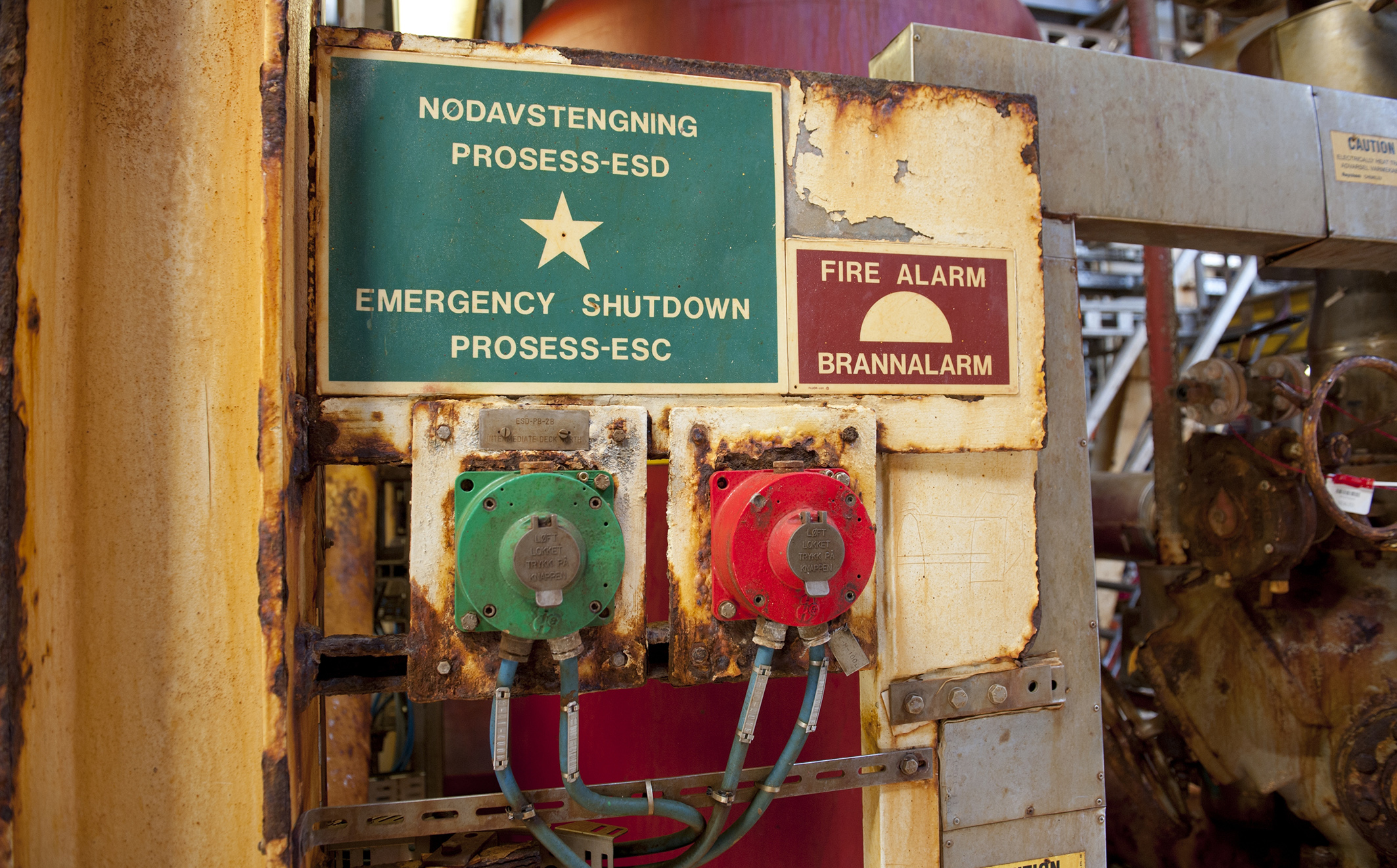
Nobody was hurt when a fire broke out in the inlet to a gas-driven compressor on Valhall’s process platform. The area was closed off and the flames extinguished within four-five minutes. Production resumed after a couple of hours.[REMOVE]Fotnote: Stavanger Aftenblad , 5 June 1985, “Brann på Valhall”.
January 1987 – methanol poisoning
The weather on Valhall was unusually cold in January 1987, when a combination of moist air and high wind corresponding to 30 degrees of frost had caused sharp cooling of decks, pipes and other gear. An unusual work accident occurred after methanol had been poured on ice covering the deck to help it thaw and aid its removal. This chemical is an effective anti-freeze because of its low freezing point, but is also a colourless and toxic liquid which can cause serious health complications and even death.
As the methanol vaporised, it was carried by the air conditioning system to an enclosed room where a man was working. The chemical paralysed his sense of smell, and he inhaled the vapour without realising this. The first symptoms of methanol poisoning soon appeared, with the worker forgetting what he was saying and hearing over the phone. He felt faint, and a colleague eventually discovered him sitting with his feet on the desk and humming.[REMOVE]Fotnote: Rasen, Bjørn (2007): LF6A. Valhall at 25 … and it’s only the beginning , p 150. After a swift transfer to the sick bay, he was dosed with ethanol – neat alcohol. Paradoxically, this acts as an antidote to methanol by slowing its absorption by the body. That in turn prevents the poison being broken down, so that it can be voided in urine and by breathing.
The nurse requisitioned more alcohol in the form of vodka from a standby ship, and spent the subsequent helicopter flight to hospital on land trying to keep the patient awake and drinking.
Tests showed that the methanol was out of his system, but that his alcohol content was so high that he had to remain under observation overnight. Fortunately, things went well and he could be discharged the following day.[REMOVE]Fotnote: Stavanger Aftenblad , 21 January 1987, “Metanolforgiftning på Valhall”.
November 1988 – gas blowout
The alarm sounded in the joint rescue coordination centre at Sola airport when a gas blowout occurred onDyvi Stena , which was engaged in exploration drilling for Amoco. Emergency preparedness was stepped up, but it was fortunately unnecessary to respond. Since the blowout was small, no evacuation of personnel from the rig was required either. Because no riser had been installed between drill floor and seabed, the gas escape failed to reach the surface. However, all drilling halted as soon as the blowout had been registered. Heavy drilling mud was pumped down the well to counterbalance the pressure and stop the gas flow.[REMOVE]Fotnote: NTB, 13 November 1988, “Gassutblåsning i Nordsjøen”. No pollution threat was posed.
A total of 272 incidents involving gas leaks of various sizes from fixed installations on the Norwegian continental shelf (NCS) were recorded in 1988-89. Only 69 were notified to the NPD, which had no explanation for the under-reporting.[REMOVE]Fotnote: Dagens Næringsliv , 30 October 1990, “Kun 69 av 272 gasslekkasjer rapportert”. These figures derive from an analysis conducted by the Petcon Consultancy on behalf of the Norwegian Oil Industry Association (OLF) and the Federation of Offshore Workers Trade Unions (OFS). Information was collected for each incident on its date, type of gas, the equipment or components involved, the kind of activity, the hazard class and the cause.
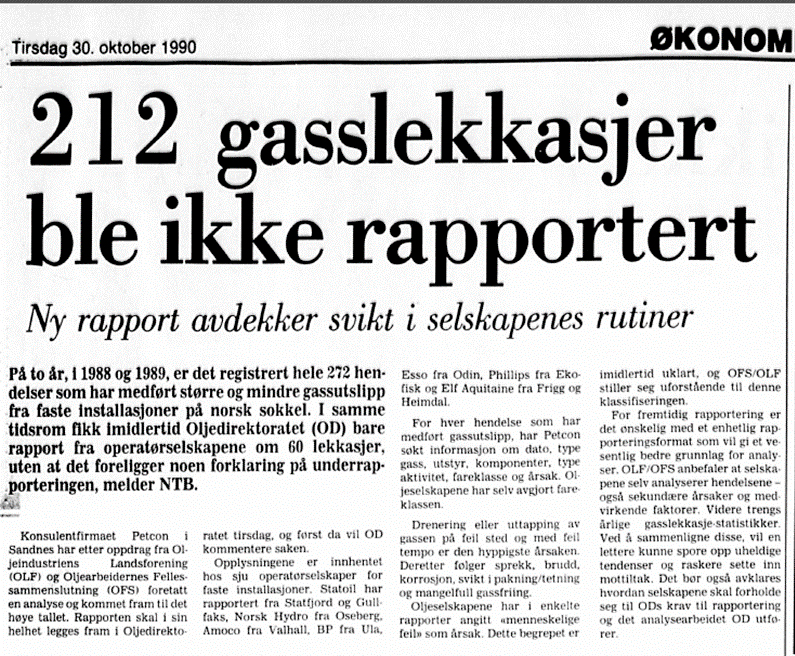
Drainage of gas from the incorrect place in the reservoir and at the wrong pace appeared to be the most frequent reasons for the discharges. Others included cracking, fractures, corrosion, failure of seals and inadequate liberation of gas. The leaks were ascribed by the oil companies in some reports to human error. That explanation was unclear, and both the OLF and the OFS found this classification to be incomprehensible.[REMOVE]Fotnote: NTB, 29 October 1990, “272 større og mindre gasslekkasjer på sokkelen på to år”.
1994 – radioactive sources
Control of a radioactive source with a radiation intensity of 15 billion becquerels was lost during downhole logging on Valhall. After four days of fishing for the stuck item, they had to give up and plug the well. This incident was not reported to the Norwegian Radiation Protection Authority, despite a licence requirement to do so immediately – and directly – in the event of any accident.
Although Baker Hughes Intec, which was doing the logging, informed operator Amoco, the radiation protection authority only received a notification from the NPD 12 days after the latter had been told. It was not the NPD’s job to pass the information on. In the wake of the incident, a new agreement was drawn up between the two state agencies to clarify the practical details of collaboration between them.[REMOVE]Fotnote: Aftenposten , 23 August 1994, “Radioaktiv avklaring fra Oljedirektoratet”.
This was the eighth accident involving radioactive substances on the NCS in 1993-94. They are used because these instruments are much more effective in identifying small amounts of oil.[REMOVE]Fotnote: Aftenposten , 18 August 1994, “Radioaktivt uhell ble ikke varslet”. The NPD conducted an audit on Valhall in 2000 to check not only BP Amoco but also subcontractors Mærsk, Baker Hughes and Schlumberger. Doubts were expressed by the regulator about BP Amoco’s competence in monitoring subcontractors using radioactive materials. It criticised the operator and Mærsk for failing to play an active part in limiting the use of such substances.
An audit on the Mærsk Guardian rig revealed that radioactive sources were stored close to explosives – a condition which led the NPD to issue a notification of order. The involvement of the management committee and the safety delegate service in the use and handling of radioactive substances was also described as deficient. BP Amoco rejected the accusation of insufficient competence.[REMOVE]Fotnote: Stavanger Aftenblad , 15 January 2000, “Radioaktiv OD-kritikk”.
Control of a radioactive substance was again lost on Valhall in 2012, when the drillstring carrying the source became stuck. Efforts to free the string were unsuccessful. Its lowest section was accordingly unscrewed in order to avoid more of the string getting stuck. The radioactive sources were left behind in the well with other equipment. The Petroleum Safety Authority Norway (PSA) characterised this incident as less serious, but nevertheless found that it represented a case of acute pollution.[REMOVE]Fotnote: Offshore.no, 10 August 2012, “Borestreng satt seg fast”.
July 1997 – discharge of hydrogen sulphide
The smell of rotten eggs spread on Mærsk Guardian after the injection of an algae-based starch caused the formation of highly toxic hydrogen sulphide (H2S) gas. Standard gas detection equipment had been installed on the jack-up rig, which was drilling on Valhall for Amoco, and this functioned as intended. The discharge site was fortunately unoccupied, so nobody was injured by breathing in the gas.[REMOVE]Fotnote: NTB, 11 July 1997, “Gassalarm på Valhall-feltet”.
December 1997 – gas intrusion
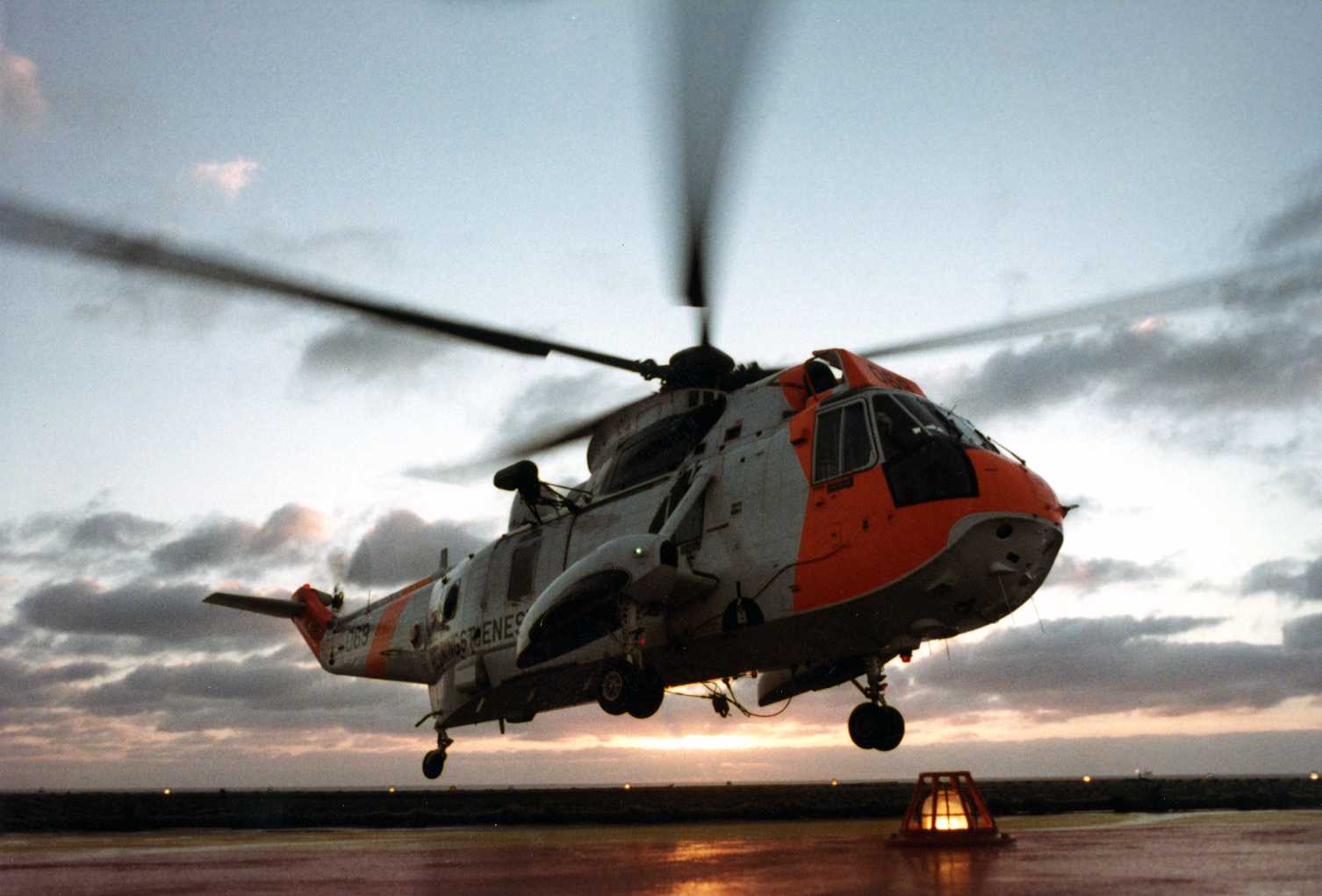
A serious gas intrusion occurred while Transocean Nordic was drilling on Valhall, requiring 30 of the 65 oil workers to be evacuated. Downhole pressure increased sharply in the middle of the night as a result of the unexpected inflow, and the threat of a gas blowout is high under such conditions.
An alert was sent at once to the joint rescue coordination centre at Stavanger’s Sola airport, which dispatched a Sea King helicopter to the rig. The NPD and the police were also notified, and Amoco immediately initiated its response plan for oil emergencies. The 35 remaining crew succeeded in stabilising the pressure from the gas intrusion and preventing an uncontrolled blowout by increasing the weight of the drilling mud in the well. Everything was back under control within a couple of hours, and the 30 evacuated workers could be flown back to the rig after a day had passed.[REMOVE]Fotnote: Dagbladet , 14 December 1997, “Tilbake etter gassdrama”.
January 1998 – injury on rig
A 20-year-old man from Jørpeland near Stavanger was injured while working on the Mærsk Guardian rig when production wells were being drilled on Valhall. After he had been crushed against a railing by a heavy length of riser pipe, a helicopter was called in from Ekofisk to take him to Rogaland Central Hospital. Doctors subjected him to an internal examination, while both the police and the NPD conducted their own investigations in line with routines for such incidents.[REMOVE]Fotnote: Stavanger Aftenblad , 15 January 1998, “20-åring alvorlig skadet etter ulykke på Valhall”.
The police inquiry revealed that the crane driver involved in lifting the riser pipe lacked the required certificate. Mærsk Contractors personnel both on land and offshore were aware of this, but failed to intervene. In addition, the crane’s operating levers had been extended in a way which contravened the regulations. The accident was caused when the driver unintentionally brushed against one of the levers. Mærsk Contractors was fined NOK 400 000 as a result of the work accident.[REMOVE]Fotnote: Stavanger Aftenblad , 23 August 2000, “Mærsk bøtlagt etter kranulykke”.
November 1999 – audit
BP Amoco was sharply criticised by the NPD in an audit report because the recently merged company was allegedly unable to document that its working environment and level of safety were unacceptable. This followed an investigation by the regulator into these aspects of a reorganisation process launched partly because of the merger and partly in order to cut costs.
“BP Amoco has failed to analyse the consequences of organisational changes made and planned offshore in the support functions on land ahead of their introduction,” the NPD found. “The company was thereby unable to document that it could maintain an acceptable level of safety on the installation.”
The company was ordered to produce “an overall review and analysis of the consequences of staffing and organisational changes made and planned in connection with the merger and parallel change processes”. At the same time, the NPD demanded that BP Amoco’s employees be involved in the analysis work. For its part, the company maintained that the restructuring processes had been “satisfactorily planned and executed”. The NPD’s investigations were not confined to BP Amoco. Several oil companies merged in this period, and audits were conducted with the Norsk Hydro-Saga Petroleum and Phillips-Conoco unifications.[REMOVE]Fotnote: Dagens Næringsliv , 27 November 1999, “Svært kritisk til BP Amoco”.
August 2000 – rust and blocked nozzles
Lack of maintenance for fire safety equipment halted production on Valhall, with rusting and blocked nozzles among the irregularities identified by a routine inspection. An abrupt shutdown is rare in the oil industry, but the safety of people working in the sector took priority. Nevertheless, none of the personnel on the field were sent ashore. Production remained at a standstill for several days, and BP Amoco had to invest in new fire safety equipment.
Local government minister Sylvia Brustad had this comment: “I feel it’s a source of concern that matters are allowed to reach such a stage that the whole platform must be shut down.
“Prevention must be pursued in this area at all times, so that we can rely on safety being 100 per cent – particularly with regard to employees in the oil sector.”[REMOVE]Fotnote: NTB, 27 August 2000, “BP stoppet oljeproduksjonen på Valhall”.
Union officials on the field were also very critical. Ingard Haugeberg, chair of the ABC house union, commented: “Failures in the fire extinguishing system are among the worst that can happen. It worries me that we don’t know how long the equipment has been non-functional.”[REMOVE]Fotnote: Stavanger Aftenblad , 29 August 2000, “Sterk kritikk av Valhall-sikkerhet”.
The Norwegian Oil and Petrochemical Workers Union (Nopef), which included the ABC, blamed safety conditions in the North Sea on the Norsok process implemented in the mid-1990s.
In the union’s view, a clear relationship existed between this Norwegian government initiative to make savings and a negative trend in offshore safety. It also believed that the oil companies had to up their game.
“It’s a disturbing signal when the NPD halts production on Valhall,” said Haugeberg. “The worst aspect is that this incident forms part of a long series of revelations which show that offshore safety is not as good as it once was.”[REMOVE]Fotnote: Stavanger Aftenbladet , 29 August 2000, “Nopef: Svekket sikkerhet er myndighetenes Ansgar”.
In connection with the discovery of blocked fire water pipes on Valhall, the OFS union raised another aspect of offshore safety – the safety bonuses given if no accidents occurred on a platform. Additional payments to management and rank-and-file on offshore installations which had achieved good safety statistics and cost cuts were increasingly common. According to Stavanger Aftenblad , a number of people on Valhall feared that such bonuses could undermine safety and lead to an overly positive picture of reality – with accidents going unreported to avoiding losing attractive rewards.
The OFS feared that platform managements were applying pressure to keep down costs in order to secure their bonuses, and that spending cuts would mean lower priority for important maintenance. BP had introduced performance contracts for both management and groups of rank-and-file workers with the aim of motivating them to avoid accidents and to pay attention to safety.[REMOVE]Fotnote: Stavanger Aftenblad , 31 August 2000, “Sikkerhetsbonus svekker sikkerheten”.
August 2003 – injury on IP
A 36-year-old scaffolding foreman fell 13.5 metres and suffered severe injuries while working on a skid beam over the drill floor on the Valhall IP injection platform. He was working with a scaffolder to disassemble equipment on scaffolding when the accident happened, and first hit a beam and then the platform deck. Both men were attached with lines and hooks because part of the work area had no grating. The foreman probably disconnected his hook in order to reach a new position.
When the equipment he was holding slipped out of his grasp, he lost his balance, fell backwards and landed on a temporary deck 13.5 metres below. The victim worked for maintenance specialist Rheinhold & Mahla Industrier. Both the PSA and the police investigated the accident.[REMOVE]Fotnote: NTB, 30 August 2003, “Alvorlig skadd etter fall på Valhall-feltet”. Although serious, the foreman’s injuries were not life-threatening. The PSA nevertheless took the view that the accident had the potential to be fatal in only marginally different circumstances.
Its investigation identified management weaknesses, including inadequate planning and communication. General work permits were used for building and demolishing scaffolding, and were rolled over without a specific assessment of risk in each case.[REMOVE]Fotnote: PSA, 7 January 2004, Gransking av fallulykke på Valhall.
December 2003 – well kicks
Control was lost over well A08B on the Valhall drilling platform (DP) on 10 December. The crew managed to re-establish control fairly quickly following this well kick, but a new and more serious incident occurred seven days later. After a period of worsening conditions and pressure build-up in the well, control was regained towards the end of December. The PSA criticised BP for doing a poor job when things went wrong.[REMOVE]Fotnote: PSA, investigation report, summary, Granskning av brønnspark i brønn 2/8-A08B Valhall DP i desember 2003. The incident was characterised as high-risk, and could have caused a blowout. According to the PSA, staffing on Valhall was too small after the kick.
Other shortcomings included unclear communication and division of responsibilities between land and offshore, along with a lack of understanding of the risk.[REMOVE]Fotnote: Stavanger Aftenblad , 23 September 2004, “Nær utblåsning på Valhall”.
January 2004 – gas leak
A gas leak occurred on Valhall after valves had undergone a maintenance check.[REMOVE]Fotnote: Stavanger Aftenblad , 13 January 2004, “Millionbot for dødsulykke”. Gas leaked from a lubrication nipple, and triggered the alarm and deluge systems. Production shut down immediately, and 154 workers crossed the bridge to the quarters platform until the position could be clarified. After just under 30 minutes, the leak had been located and stopped, and work began five hours later to bring the facility back on stream.
BP’s own investigation team was joined by representatives from the PSA and the police, who flew out to Valhall to determine what had occurred.[REMOVE]Fotnote: Stavanger Aftenblad , 13 January 2004, “154 ble evakuert på Valhall-feltet: Produksjonen er i gang igjen”. According to the PSA, the nipple should have been replaced during a maintenance campaign two years earlier but was not defined as sufficiently critical. Moreover, it found that the relevant job had not been adequately planned on the basis of the error scenarios which might have arisen.[REMOVE]Fotnote: Offshore.no , 18 February 2004, “Gransking av gasslekkasje på Valhall”.
April 2004 – injury on rig
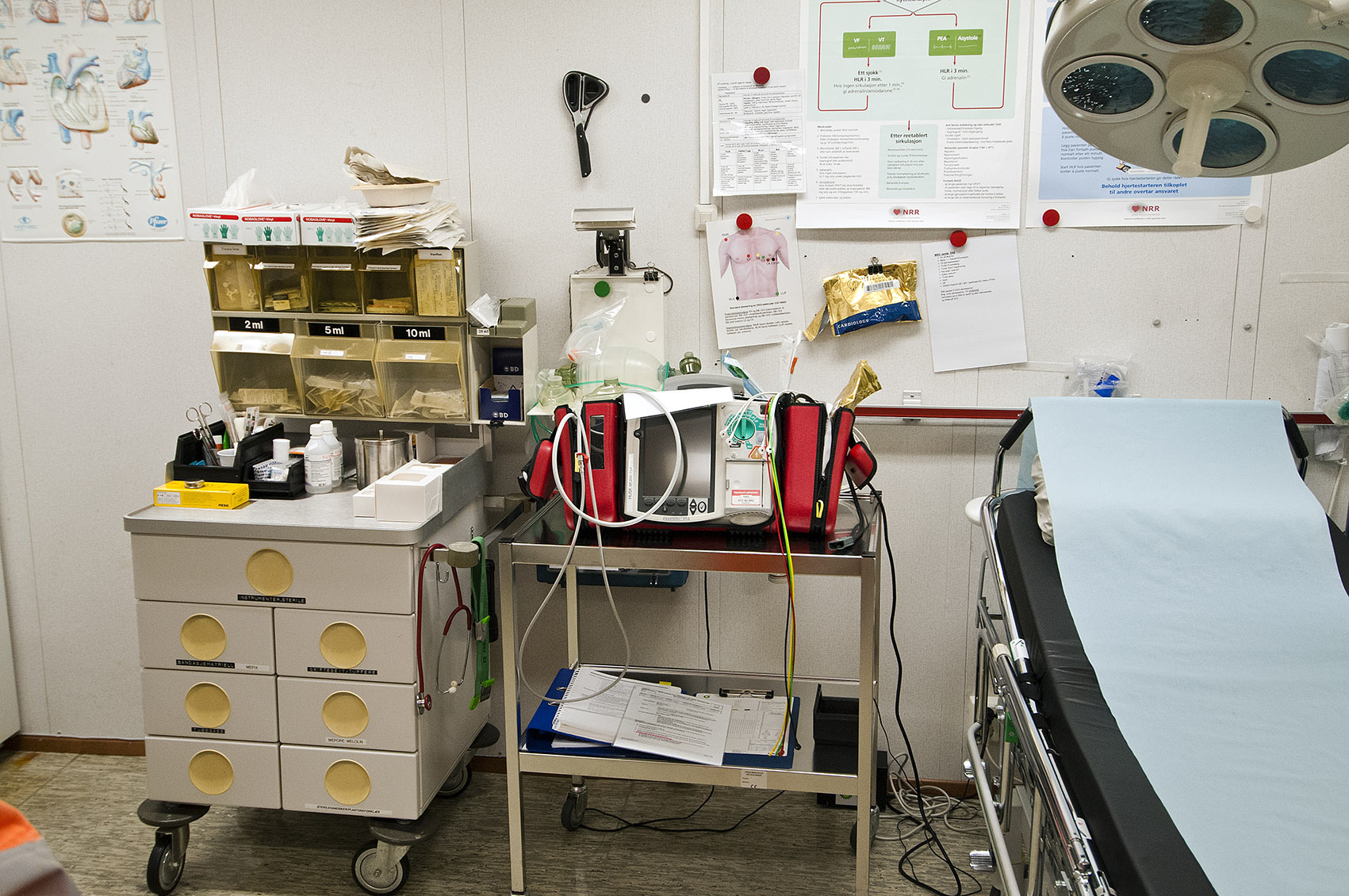
A 33-year-old employee of Schlumberger Well Service was badly injured on the West Epsilon rig during drilling on Valhall, when a steel plate weighing 357 kilograms fell 15 metres and struck him on the thigh. He also suffered facial injuries.The accident happened during a lifting operation with a telescopic crane. This struck a hatch cover and caused it to fall from the rig’s cellar deck onto Valhall’s north flank platform, where two people were standing. Investigators from the police, the PSA and BP flew out.[REMOVE]Fotnote: Stavanger Aftenblad , 3 April 2004, “Alvorlig for 33-åringen etter Valhall-ulykke”. Conditions identified by the PSA prompted it to order BP to stop using the crane type responsible for the accident at once.
The safety regulator seldom issues an immediate prohibition of this kind, but it found the position to be so serious that instant action was required. According to the PSA, problems on the platform embraced procedures, documentation and understanding of the risk. The victim was only centimetres from death.
The order required BP to check and update the crane, requirements for expertise were imposed, and checks had to be carried out on similar equipment on other BP platforms. The company had to confirm compliance with these terms before the cranes could be taken back into use.[REMOVE]Fotnote: Stavanger Aftenblad , 20 April 2004, “BP får pålegg etter Valhall-ulykke”. It transpired that parts of the crane’s safety system, including the anti-collision system, were not working. Nor were the window wipers in the crane cabin, so that visibility was poor in the dawn light when the accident happened. Moreover, the hatch cover which fell down had not been secured with additional chains.
BP was sharply criticised by the PSA after the accident. Although several factors contributed to this mishap, they all related to “serious failures in BP’s management system”. Notifications for four other orders were also issued, requiring BP to ensure the necessary crewing and expertise for crane operation both on land and offshore. The company was also told to verify its system for monitoring how contractors carried out their work and complied with the health, safety and environmental (HSE) regulations.
A further requirement was to follow up and continue developing BP’s management system and to ensure that changes to projects were followed up during testing and commissioning. Finally, the company was ordered to check management systems at its suppliers, so that testing and commissioning were carried out, and to make sure the necessary documentation was available before start-up.[REMOVE]Fotnote: Stavanger Aftenblad , 22 June 2004, “Tilsyn med pålegg til BP”.
July 2011 – fire on PCP
Inadequate maintenance was the PSA’s verdict on a fire which broke out in the compressor on Valhall’s process and compression platform (PCP) on 13 July. A shaft fracture on a cooling pump in a crane engine room was the immediate cause. The engine lost coolant circulation, causing a minor blaze to break out. Red-hot particles from the exhaust vent were blown across to ignite flammable gases emerging from a vent stack for the compression modules.[REMOVE]Fotnote: PSA, Investigation report: fire on Valhall PCP on 13 July 2011 , 4 January 2012.
A glowing cinder about the size of thumbnail floating onto the bridge between the PCP and the WP was the first indication of the fire to be noticed. The person who saw it reported the incident to the senior mechanic, who in turn saw flames two metres high in the vent stack. White smoke was also blowing from the crane’s exhaust vent while it was in use. This was immediately reported to the central control room (CCR). Instead of initiating a general fire alarm, however, the latter asked the area technician to check the position. Only when the blaze was confirmed to be genuine was a general alarm sounded. No alarms were triggered by smoke or heat from the fire.
The crane driver had received no signals that anything was amiss when the CCR initiated an equipment shutdown, and accordingly went to check why the engines had stopped. Through the blue-black smoke filling the engine room, he saw a small flame from the diesel injector for one engine. He succeeded in extinguishing this with the aid of a glove. But the heat, possibly combined with an increase in exhaust fumes as a result of entrained water vapour, caused red-hot particles to be blown out from the engine’s combined spark arrestor and silencer. The latter devices had more or less rusted away. It subsequently transpired that the spark arrestor was not classified as safety-critical equipment and accordingly had no maintenance programme.[REMOVE]Fotnote: PSA, Investigation report: fire on Valhall PCP on 13 July 2011 , 4 January 2012.
According to the PSA, ensuring that this device functioned was crucial and its failure increased the probability of igniting leaks from the gas coolers – an incident with major accident potential. The wind had blown red-hot particles from the exhaust vent over to the vent stack for flammable gases from the compressors, causing the gases to ignite. This could have had major consequences. If the crane engines had not been shut down, the blaze in the engine room could have developed into a diesel fire.
That would have caused piping for the diesel injectors to rupture and spray diesel oil on the exhaust manifold, leading to a much bigger conflagration and making it hard to evacuate the crane. The only escape route was a ladder next to the engine room door. It proved difficult to put out the fire in the vent stack. No automatic extinguishing systems covered the area, and it was considered too risky to send in personnel with hoses. No assessment of how to fight a fire there had been made, so it was decided to deploy a standby ship with FiFi water monitors to spray water on the flames.
The fire was extinguished in just over 90 minutes, but no standby ship with FiFi monitors was included in the emergency response plan for Valhall. Although nobody suffered physical injury, the PSA considered that the fire could have led under slightly different circumstances to a serious condition on the platform.[REMOVE]Fotnote: PSA, Investigation report: fire on Valhall PCP on 13 July 2011 , 4 January 2012. Production from Valhall was suspended for nine and a half weeks as a result of the incident.[REMOVE]Fotnote: Stavanger Aftenblad , 13 July 2011, “Brann på Valhall”.
Read more in the article entitled “Fire on PCP – a reflection of old installations?”
July 2011 – well kick
BP lost control on 22 July of a well being drilled to store cuttings and other waste on Valhall when gas suddenly intruded into the borehole. This kick was remedied by pumping “kill mud” into the well so that the gas could be circulated out. Another serious incident had arisen only days before in the same well, when a leak occurred through the cemented casing in the well. A pressure test showed that this involved one-two barrels per hour. Both incidents were classified at the most serious level, described as a “serious weakening or failure of safety functions or other barriers, so that the facility’s integrity is at risk”.[REMOVE]Fotnote: Dagens Næringsliv , 29 August 2011, “Mistet kontroll over Nordsjø-brønn”.
November 2013 – serious nonconformities
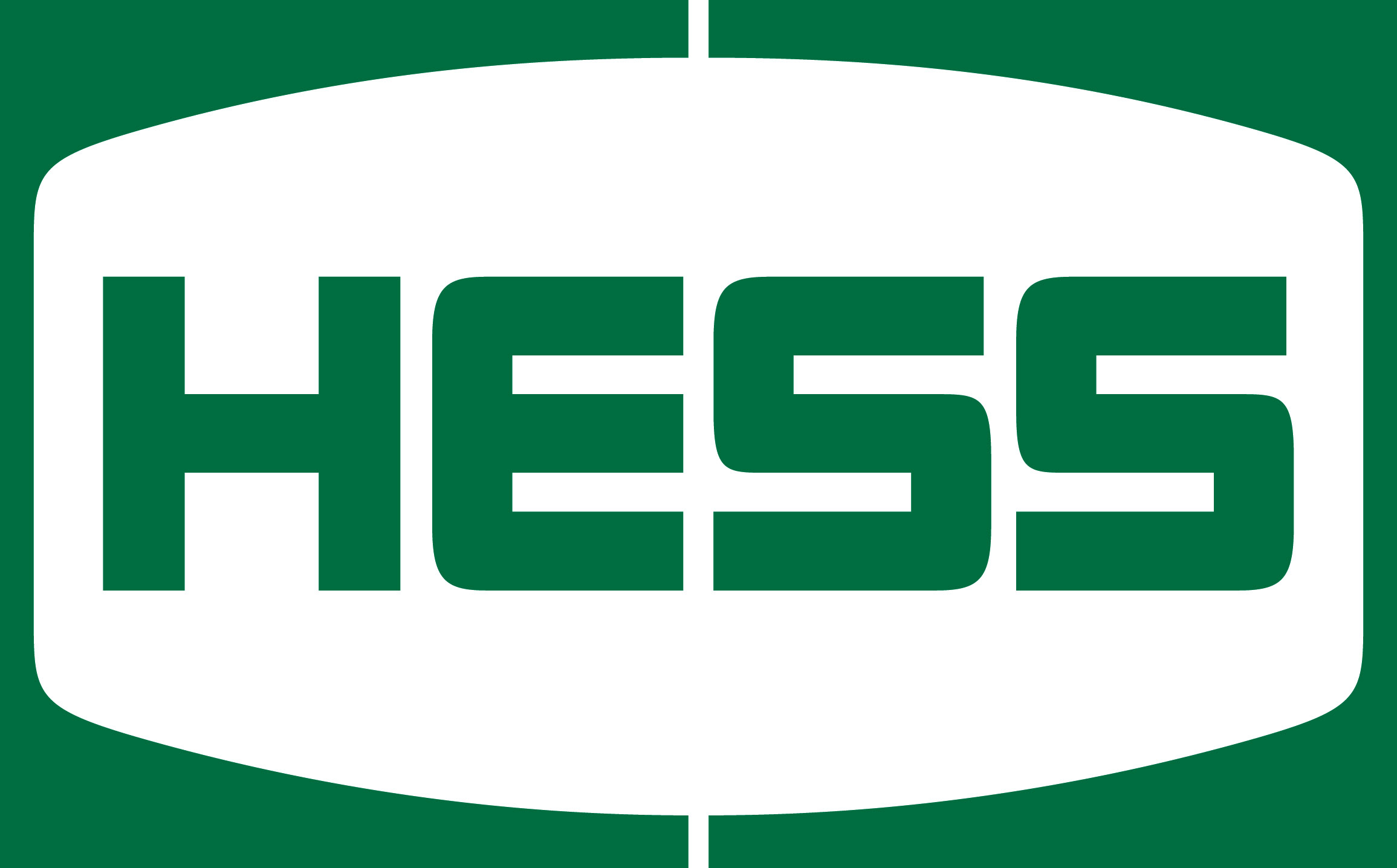
Valhall licensee Hess Norge AS was ordered by the PSA to conduct a full review of its management and documentation systems after an audit had found what were described as serious nonconformities. Issues related to organisation, management, documentation and handling of risk were key components in the audit. This revealed that Hess had serious deficiencies in its management of the business and failed to satisfy regulatory requirements. Hess was the first licensee without operator responsibilities to be audited by the PSA after it had developed a method for supervising such companies.
Hess has an interest of about 64 per cent in Valhall, with operator BP holding the remaining 36 per cent. The US company has been a player in Norway’s oil and gas sector since activity started in 1965, but with varying levels of involvement and organisation. It moved its head office back to Stavanger in 2007 after a period in Oslo, primarily to get closer to its partners and the broader petroleum community. The PSA’s audit identified three nonconformities related to the company’s management system, its handling of risk and its documentation system.
Hess was found to lack such fundamental capabilities as a functioning management system to meet HSE requirements, and was unfamiliar with the basis for its own risk management system. In addition, the absence of a documentation system meant that it was unable to trace old documents and thereby establish what it had done earlier.[REMOVE]Fotnote: Teknisk Ukeblad , 13 January 2014, “Petroleumstilsynet fant ‘alvorlige’ HMS-avvik på Valhall”.
The PSA also identified an improvement potential in relation to the dual role which licensees are meant to play in a production licence.[REMOVE]Fotnote: PSA audit report, 14 November 2013, Tilsyn med Hess som rettighetshaver i Valhall utvinningstillatelsen. Pursuant to the framework HSE regulations, the PSA ordered Hess to conduct a full review of the regulatory requirements concerning the management of activities and to implement measures to fulfil these requirements in its own activities. The company was given until May 2014 to comply with this order, and the PSA was to be notified when the work had been carried out.[REMOVE]Fotnote: PSA, 20 December 2013, Pålegg gis etter tilsyn med Hess som rettighetshaver.
2014 – quarters platform shut down
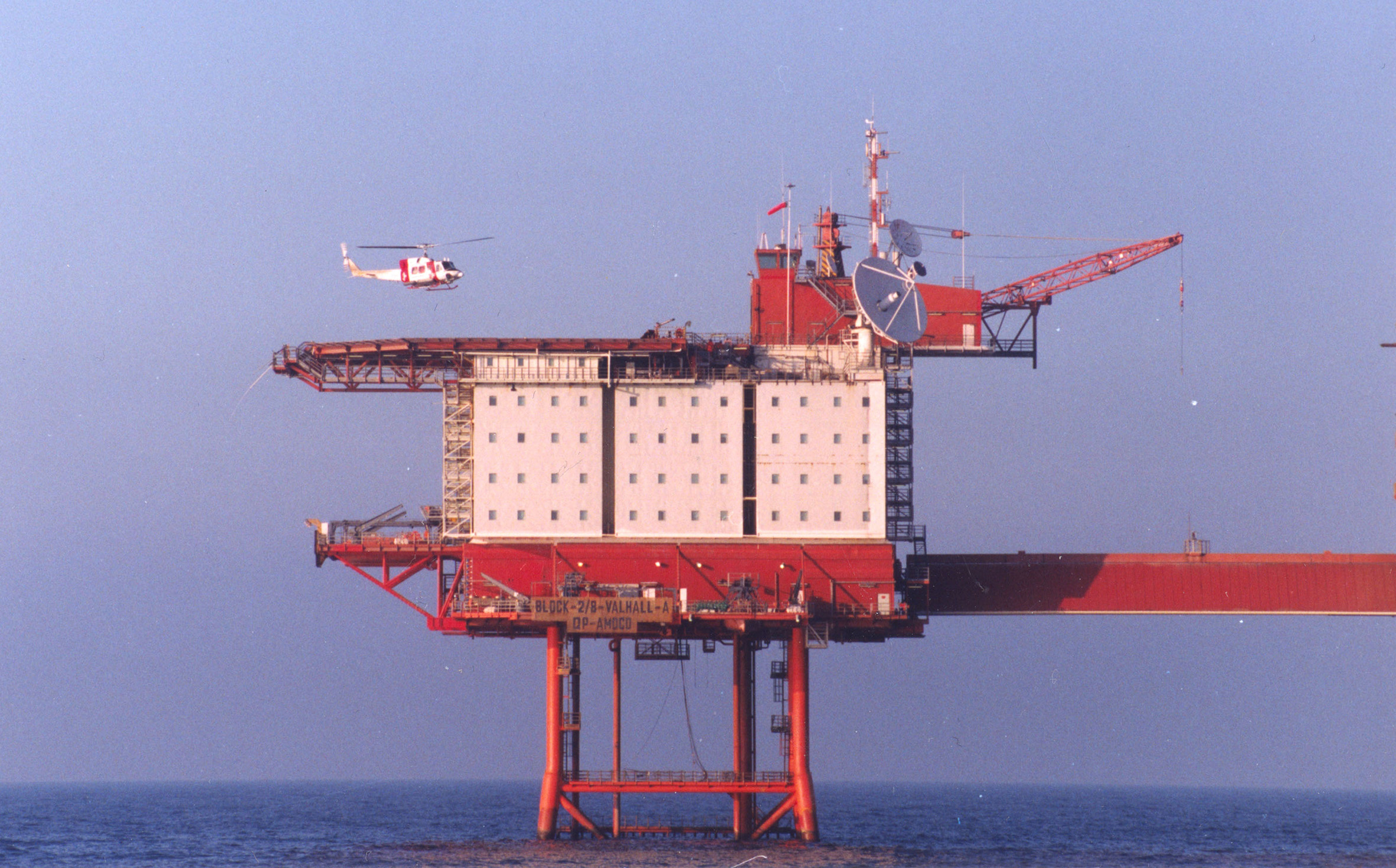
The PSA decided in December 2014 that the quarters platform (QP) on Valhall had to shut down during the winter following a study which found that it could collapse if struck by high waves. This assessment by Sintef and Marintek indicated that the risk of a wave which could threaten the QP’s structural integrity was higher in November-March than Norway’s offshore regulations permitted.[REMOVE]Fotnote: Offshore.no , 12 December 2014, “BP-plattform kan måtte stenge”.
The oldest platforms on Valhall, standing at the southernmost end of the NCS, had been installed 34 years earlier. Seabed subsidence meant that their topsides were closer than before to the waves, and that the required air gap no longer existed. A high level of activity on Valhall meant that BP needed accommodation capacity, but fewer people could work there if the number of berths was reduced.
The cost of closing the QP and acquiring a flotel to provide alternative berths meant that it and its partner, Hess, had to lower their ambitions for the field.[REMOVE]Fotnote: Offshore.no , 19 December 2014, “Får ikke forlenget levetid”.


